Safety
Minnesota Rural Electric Association helps create a cooperative culture of safety. We work closely with our member electric cooperatives to provide foundational safety education and training.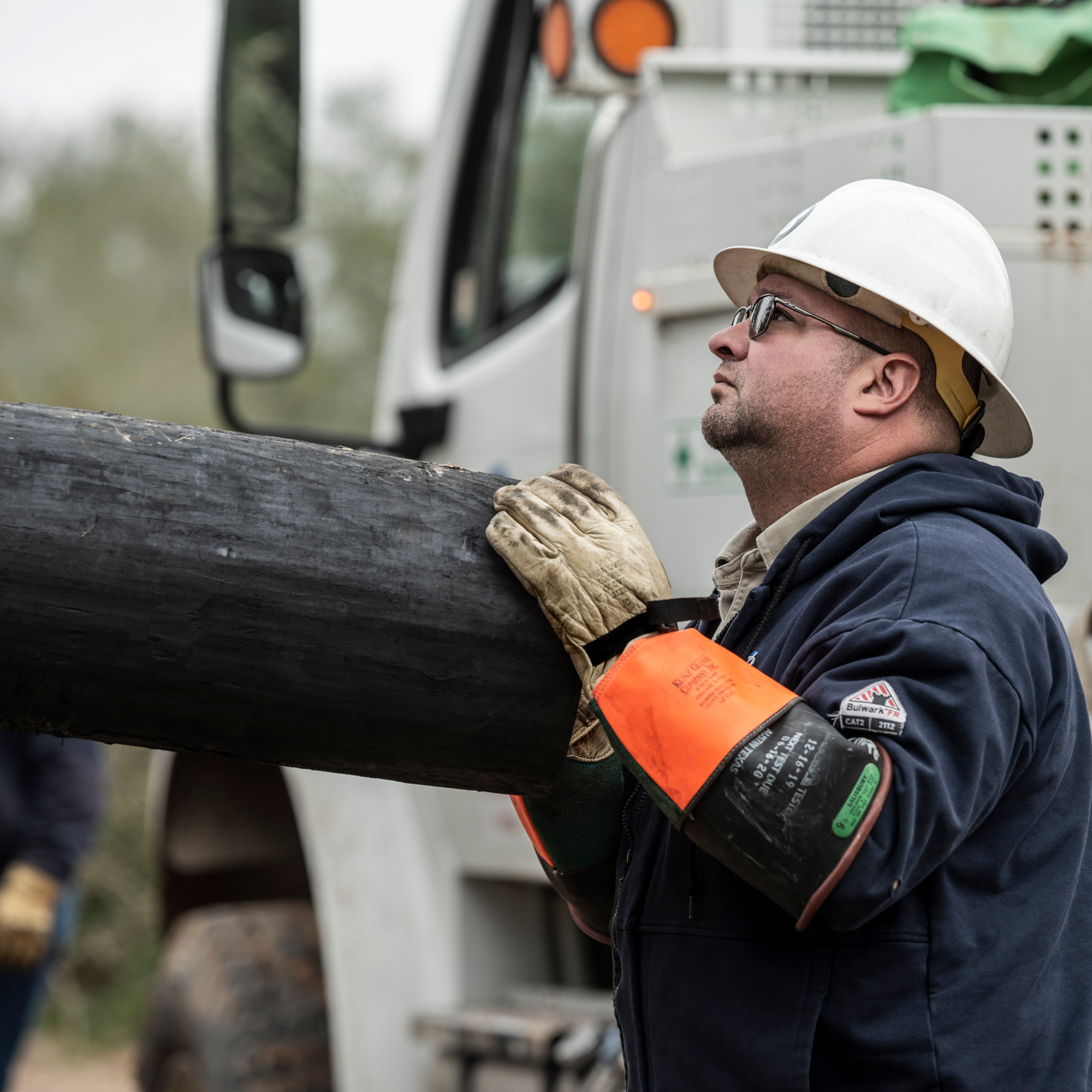
Culture of Safety
Safety is foundational for Minnesota’s electric cooperatives. We incorporate safety into everything we do.
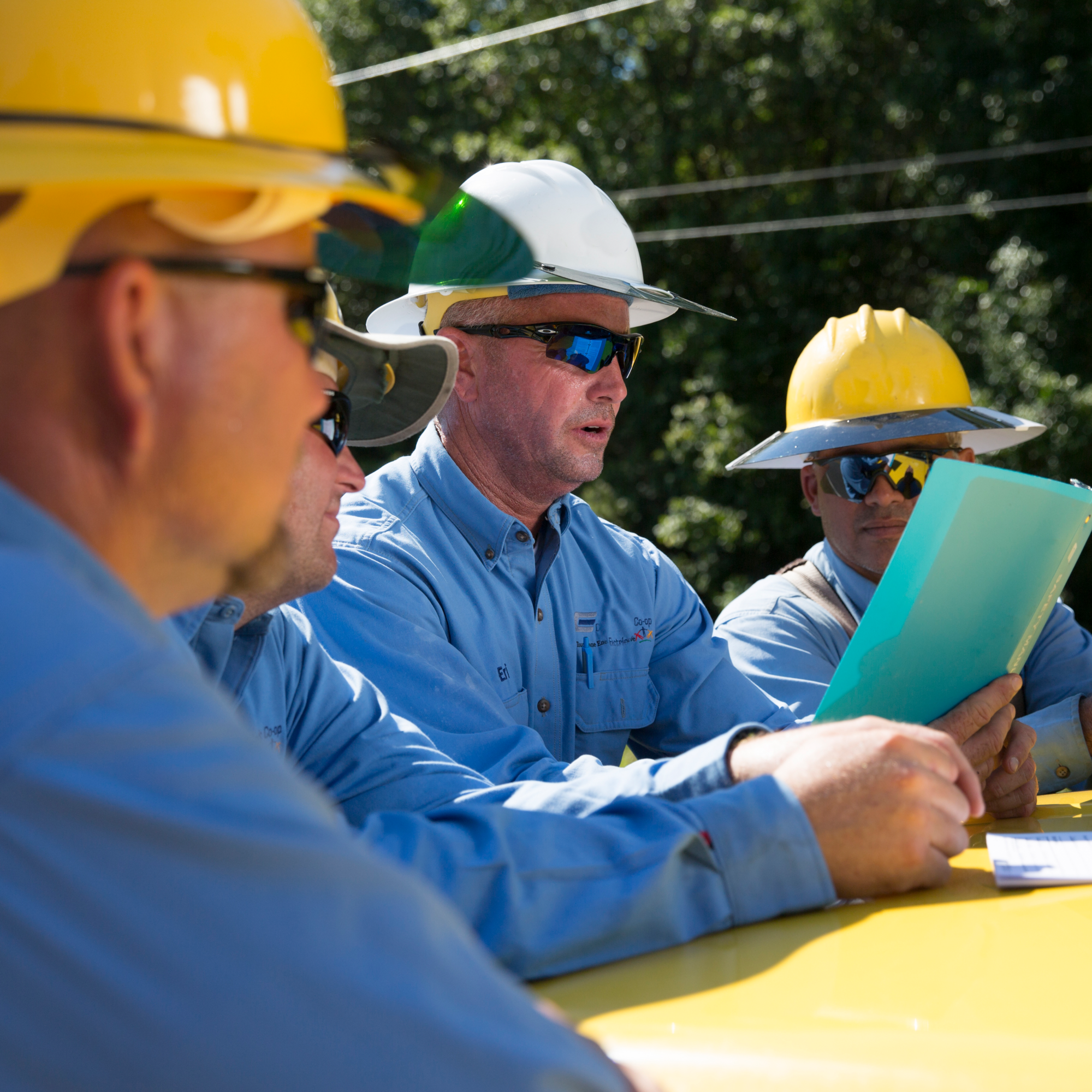
Education
MREA p
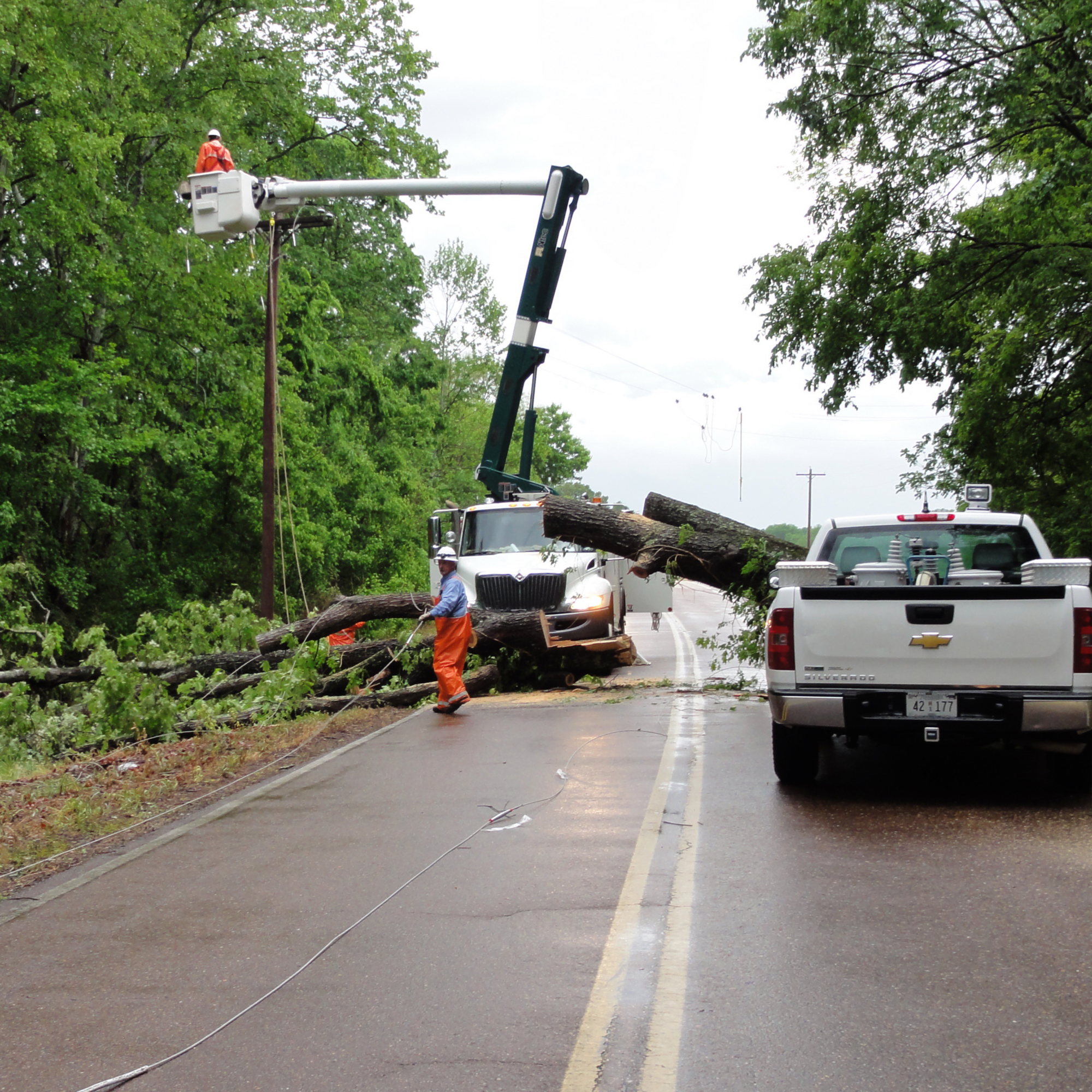
Community Safety
Not only do cooperatives value safety for their employees and members, but also the community in which they belong.
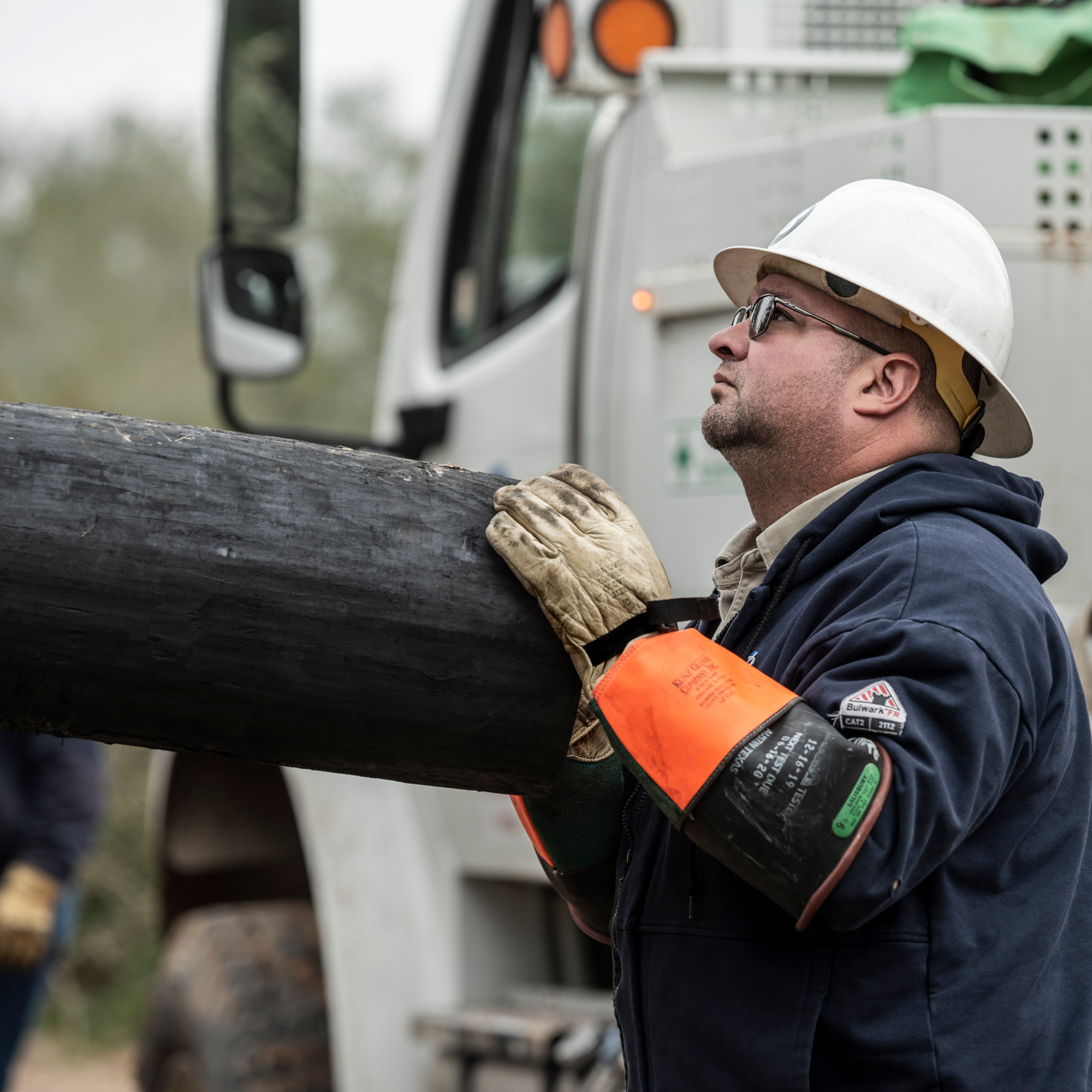
Culture of Safety
Safety is foundational for Minnesota’s electric cooperatives. We incorporate safety into everything we do.
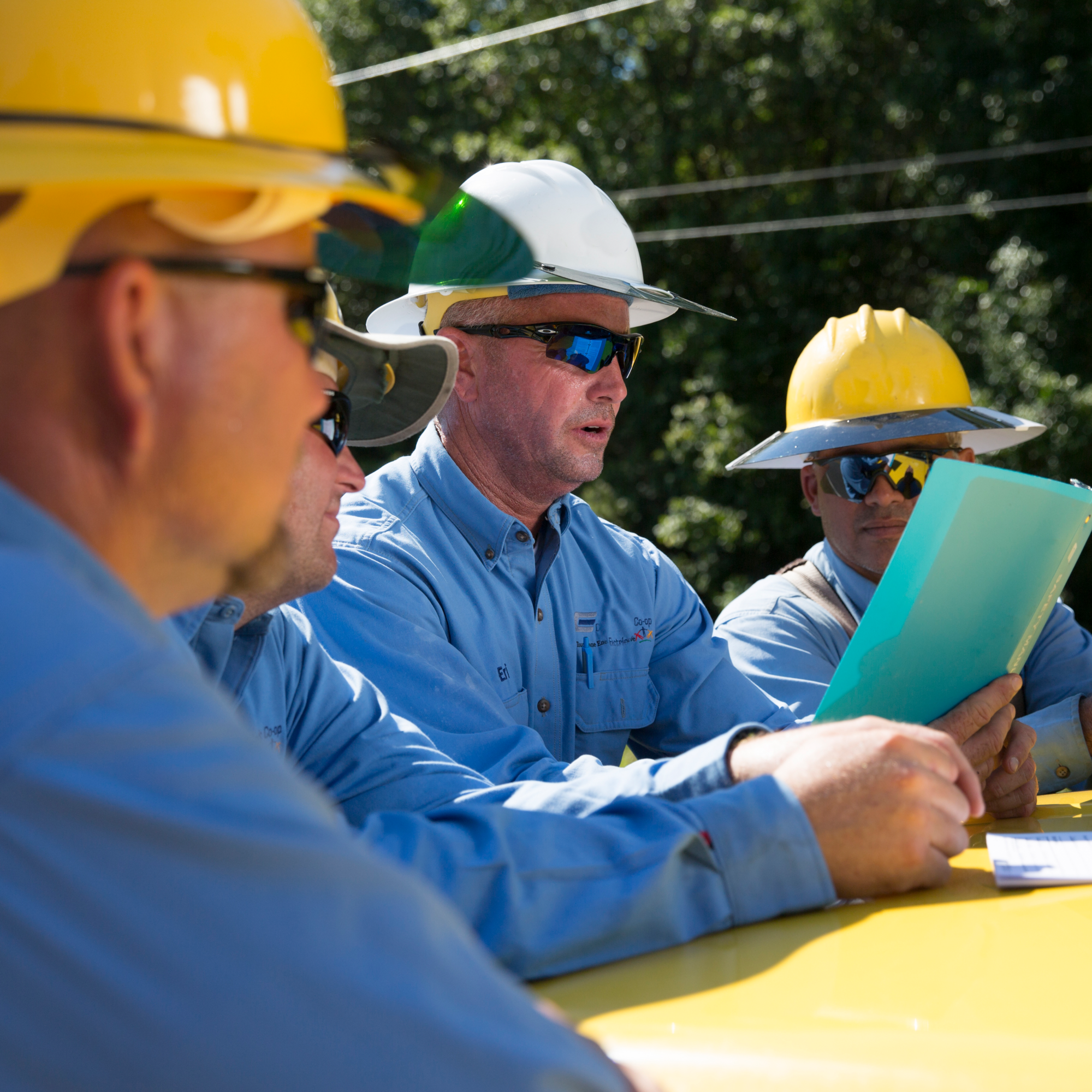
Education
MREA p
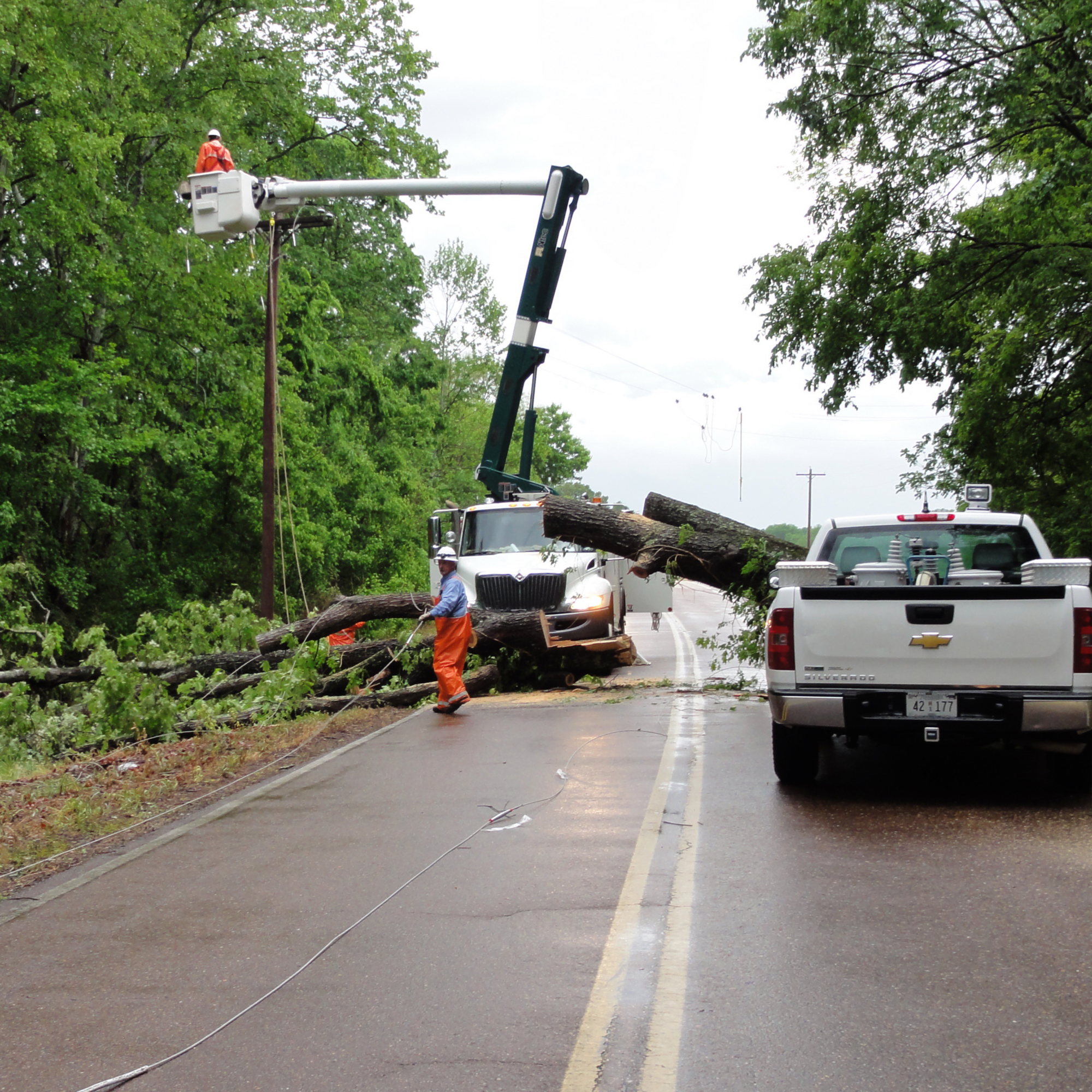
Community Safety
Not only do cooperatives value safety for their employees and members, but also the community in which they belong.
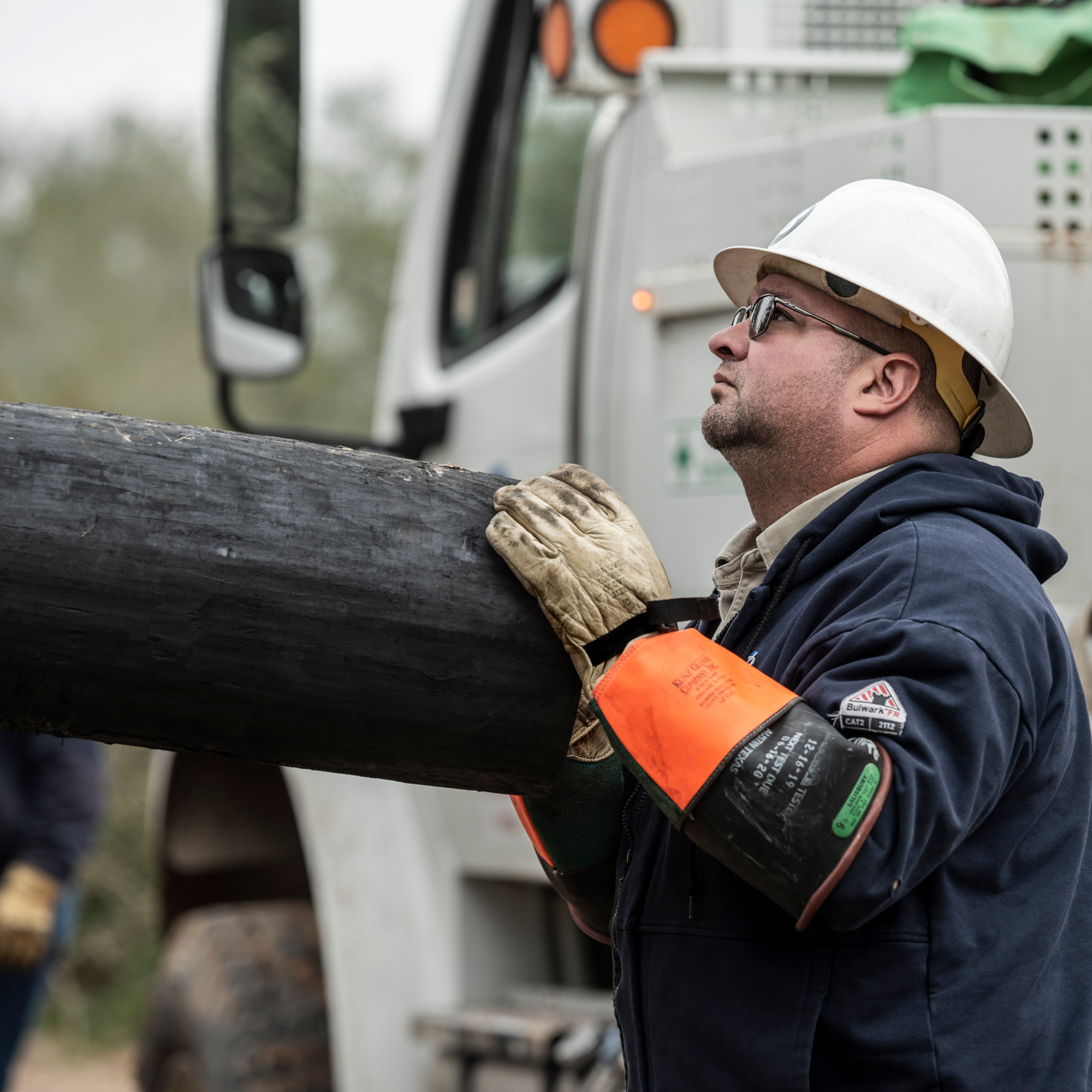
Culture of Safety
Safety is foundational for Minnesota’s electric cooperatives. We incorporate safety into everything we do.
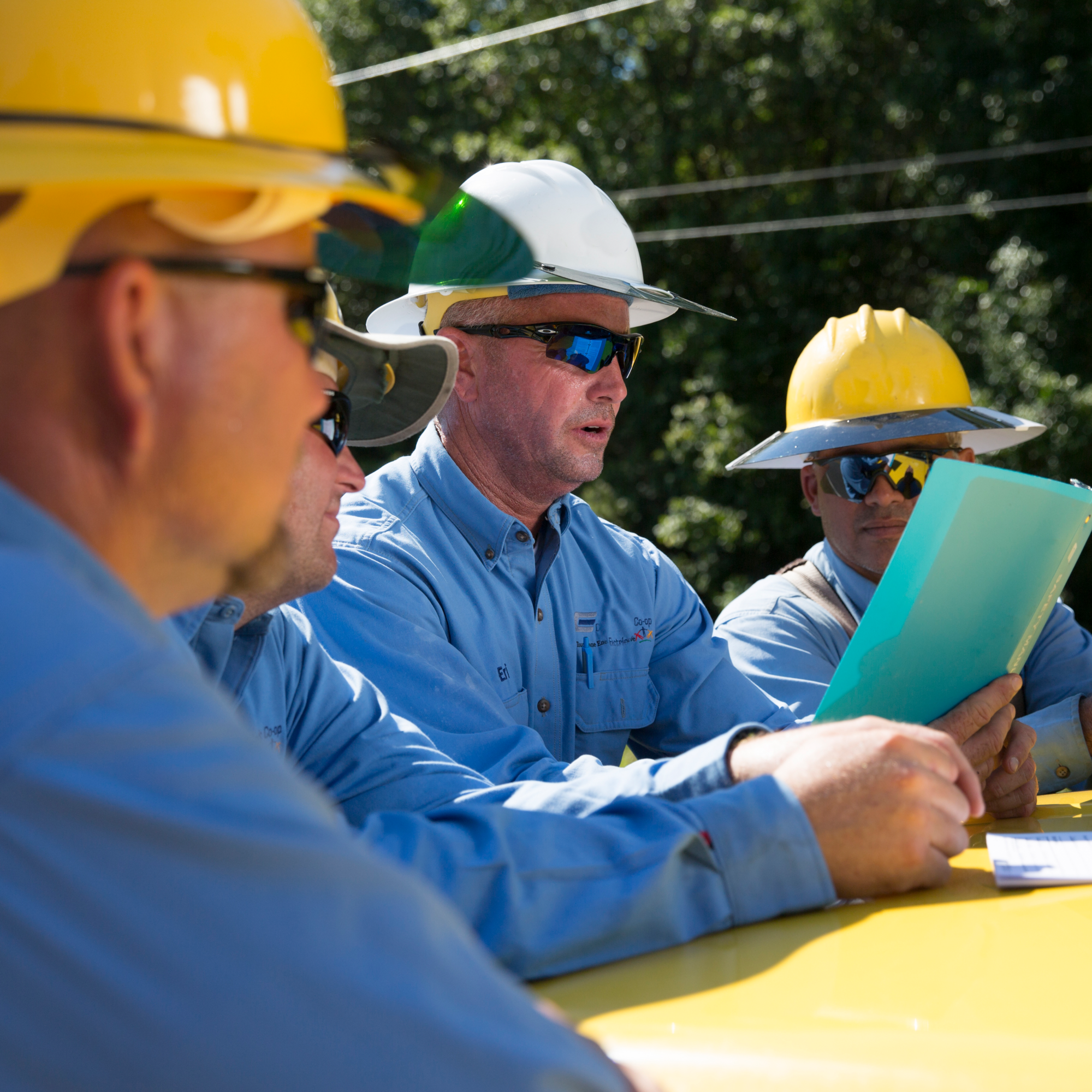
Education
MREA p
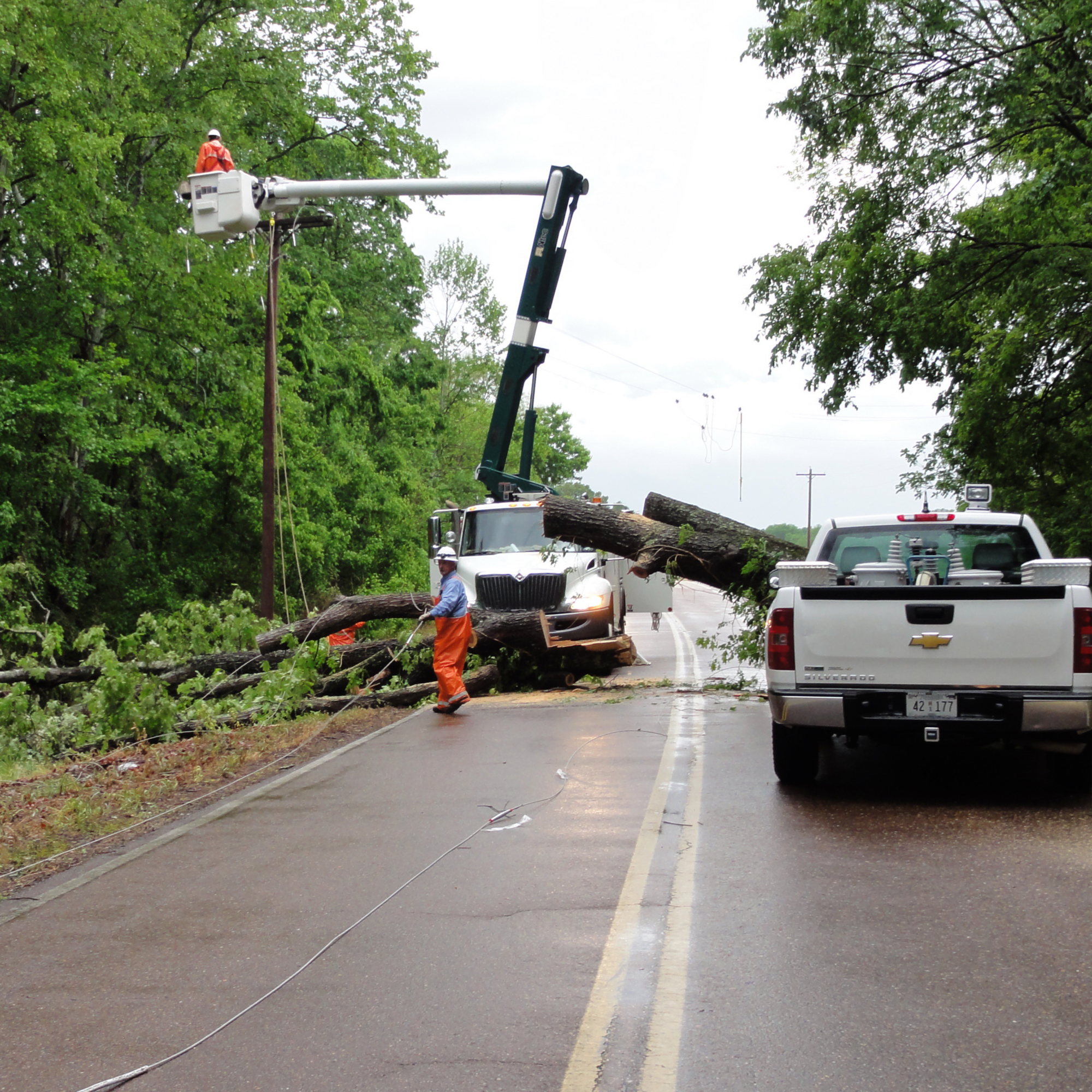
Community Safety
Not only do cooperatives value safety for their employees and members, but also the community in which they belong.
Training
MREA provides continuing education in safety to Minnesota’s electric cooperatives to help everyone get home safely.
Safety training is vital to preventing utility line work accidents. Minnesota’s electric cooperatives continuously educate and train on safety and share electrical safety tips with the community.
Our safety specialists are on-site to work with electric cooperatives and strengthen their safety culture. Through safety training, safety meetings, crew observations, random safe acts, and inspections are offered to uphold our safety standard.
We are constantly improving safety training as technology advances.
Public Safety
Home Electrical Safety
Electricity has become such a necessary part of our lives that we tend to take it for granted, but using it safely is vitally important.
Traffic Safety
If you’re driving and approach a utility vehicle stopped on the shoulder with its flashing lights activated, keep everyone safe by moving over and slowing down.
First Responders
811 - Call before you dig
Mutual Aid
While electric cooperatives provide reliable electric service to members, outages from weather and other events are inevitable. It is in our cooperative principles to collaborate with other cooperatives in times of need.
Minnesota Rural Electric Association is part a group of individuals from the statewide organizations and cooperatives across the United States called the National Storm Coordinators. This group coordinates regional, district and national support for emergency assistance involving electrical distribution and transmission.
To report an outage, please contact your local electric cooperative.